Cladding board end joints: butt together or leave a gap?
The forthcoming British Standard on cladding installation – BS 8605 part 2, will advise designers to consider minimizing features that might increase the effects of weathering, butt joints between board ends being an example.
- BS 8605 part 2 -
Vertical Cladding
If unpainted vertical boards are butt jointed - the ends butted up together - water is held in the joint and you can get rapid staining at the joint with an increased risk of rot. However, the staining becomes less obvious over time as the rest of the board weathers.
Some guidance in Finland recommends that vertical boards are crosscut, producing a chamfer on the back, with a steeper angle on the bottom end of the board than the top. That way when the boards are butted together, they meet at the front face but there is a v shaped gap behind for ventilation (see illustration). However, this is fiddly and may leave the thinner part of the board ends more prone to splitting.
Leaving a gap of 5 mm between unpainted board ends can definitely help with drainage (particularly if the boards are crosscut at a slope so that they drain outwards). The top edges (end grain) of the lower boards can also be sealed to protect them.
If the cladding boards are painted with a protective coating, providing that the board ends are painted too and the coating is adequately maintained, butt joints are not an issue.
Horizontal Cladding
The same issues can occur with horizontal boards, however there is a greater risk of water entrapment at the base of a 5mm gap joint, particularly if the boards are T&G.
Recommended Norwegian practice is to butt joint the boards, but they usually paint their cladding and so staining is not a concern.
In Summary
A 5 mm gap does have slight benefits in some cases but, as it may be considered unsightly and fiddly to construct, it’s a recommendation that installers rarely follow.
The issue can be avoided altogether by using longer length boards or finger jointed boards.
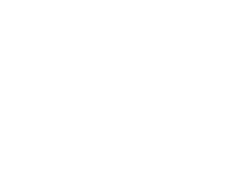